Beer, Supply Chain and How Industry 4.0 Has Changed Everything
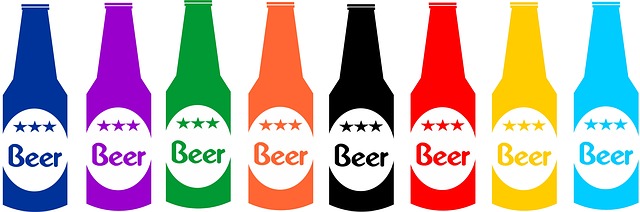
The scope and impacts of Industry 4.0 are quite wide and are often referred to across many information channels. Recently, McKinsey’s claim that Industry 4.0 brings 20 – 50% reduction in equipment costs has emerged on social networks.
Beer and Revolution
To illustrate the effect of the last industrial revolution, we will use the textbook case of the so-called beer game.
Beer game is a popular simulation game created by a group of professors at the MIT Sloan School of Management in the 1960s. It is based on a supply chain example and includes the role of a manufacturer (brewery), distributor (supplies wholesale), wholesaler and innkeeper who sells beer to end customers. The game is used to demonstrate various aspects of supply chain management. All of these elements execute each other’s orders with the aim of achieving the shortest possible time and the lowest possible cost. With this experiment, it is possible to identify individual aspects of the participants’ behavior that cause the so-called bullwhip effect, as well as to identify activities that mitigate this effect.
Subsequently, Beer game has become a subject of many academic and consultant analyses, with the goal to explain supply chain inefficiencies. The main problem was lack of transparency in the process, feedback and aspects of behavior, which was influenced by the competition, of individual players who sought to maximize profits throughout the whole supply chain.
Will the Next 50 Years Bring Some Changes?
It sure will. With a number of groundbreaking technologies, Industry 4.0 offers significant enhancements for the entire supply chain, as well as its individual elements. There is even the potential to fundamentally change existing business models.
Smart factories, connectivity related to the Internet of Things and advanced analytics are an integral part of Industry 4.0 and Digital Revolution.
So How Did Industry 4.0 Change Beer Game?
Although at some degree, automation has come to the brewery level some time ago, the need for IoT – such as sensors, data processing and cloud solutions – means that the brewery has the opportunity to make breakthrough improvements in terms of its processes and products. Process speed and product quality can be enhanced in real time by using advanced analytical and predictive tools and self-learning processes. The manufacturer’s dilemma of which technologies and procedures to give priority to can be quickly and elegantly handled with simulation technologies that will help them find the optimal solution.
At the logistics level of the supply chain, autonomous systems and vehicles are gradually being implemented. In real time, they can choose the optimal route for shipment transport with regard to traffic status information and the speed and cost balance of each route option.
At the bar lever (retail), it is possible to predict beer consumption depending on historical data and other environmental influences, for example including those outside the business (like weather).
But the Supply Chain as a Whole Shall Await the Biggest Changes
However, supply chains will increase their efficiency by gaining a much better overview of the overall delivery process and sharing real-time data between process actors. Maximum process transparency will help create a collaborative model, increase productivity and reduce risks.
Related articles
Jun 7, 2024
DJI introduces its first delivery drone
DJI introduces its first delivery drone
Jun 7, 2024
5 expert insights into the world of dynamic simulations and logistics
5 expert insights into the world of dynamic simulations and logistics
Apr 2, 2024