Enviropol – Location of the new line
The case study in pdf can download here.
APPLICATION:
The aim of the project was the design of location of the new line for processing of plastics waste. It was necessary to assess all manipulations with respect to:
- location of line of plastics
- location of the warehouse of incoming electrical waste
- storage of all produce fractions containing colored metals, iron and plastics
Necessary stores were assessed with respect to failures of individual types of technologies.
BRANCH:
Processing of electric waste
SECTOR:
Production
BENEFIT:
By using dynamic simulations we considered variants of locations of new plants for plastic processing. We compared the demands of manipulations for each of variant. In-process reserves were compared for possible failures of individual technologies.
About the company
Enviropol is a Czech company engaged in the processing of electrical waste. The company in 2015 in Jihlava launched the most technologically advanced plant for processing of electrical waste in Europe. This year, the company achieved significant success. Association of CZECH TOP 100 has chosen this company among the 70 most interesting companies.
Project targets
Outcome of the project was to assess variants of location of new lines for processing electrical waste in the existing company premises. Important output was the comparison of manipulations of individual variants. Another outcome was the setting of the size of the necessary interoperable storage in case of failure of any part of the production.
Solution
The first task was to build a simulation model of the production line. This problem was specific. Each production facility sort out a certain percentage of one faction. This percentages were referenced to the whole. Therefore this calculation had to be specific for each production facility.
Into the built model it was necessary to add handling equipment. Then we put parameterization of handling. Then it was necessary to specify paths for industrial trucks.
Then they were examined variants of location of new line of plastic. After the simulation, it was necessary to process the results.
Results
For each variant, we specified relevant outputs. We compared these individual variants by using these outputs.
The first output was the size of the buffer stock. These stocks are caused either by different speed of parts of the line, or because of their failure.
Another result was the development of individual output fractions.
The last monitored output for comparison of the options was utilization of handling equipment.
Individual variants were compared on the basis of these defined outputs. Finally, we selected three final proposals. After comparison of utilization of handling equipment, was chosen the winner.
With the help of dynamic simulation were verified three final variants. By using static calculations we did not come to so correct score. Customer could evaluate each variant due to this precise calculation. On this basis, he was able to make a better decision.
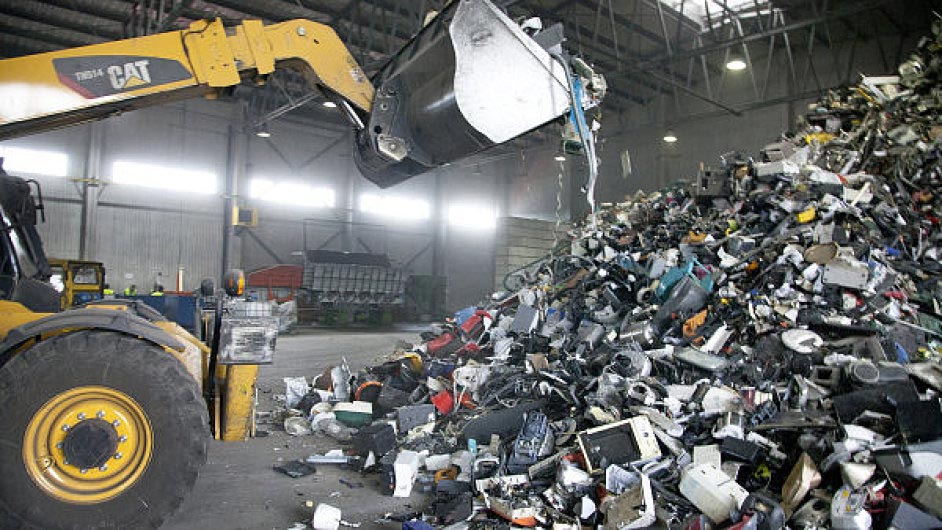
The case study in pdf can download here. APPLICATION: The aim of the project was the design of location of the new line for processing of plastics waste. It was necessary to assess all manipulations with respect to: location of line of plastics location of the warehouse of incoming electrical waste storage of all produce […]