Lucas Varity Ltd.
The case study you can download here
APPLICATION:
Logistic processes optimization
BRANCH:
Developement, production, and sales of hydraulic brakes
SECTOR:
Handling
BENEFIT:
Using the dynamic simulation model in Witness it has been created elimination of some handover places and vehicles number in production with the consequence in decrease of handling and operational costs.
Performing these changes it has been achieved savings in the amount of 245 000 CZK per month and at the same tim 15 hours of forklifts work per week.
About the company
TRW Automotive is one of the front suppliers of car accessories. The company is focused on production of disc brakes and it is a leader on european market. It supplies brake systems to prime world car factories. The company was established in 1999 and it is located in Jablonec nad Nisou.
Project targets
The project goal was on the analysis basis of the current state (material flows, storage capacity, handling capacity, finding out of utilization of handlig technology and workers) a proposal of logistic processes optimization in Lucas Varity Ltd. with the focus to remove bottlenecks and operational cost reduction of 10%.
Solution
On the basis of input data from Lucas Varity Ltd. it has beed created dynamic simulation model of handling and storage. This model has been cretaed to fullfil predeterminated rules for all types of handlig technology, all handover places, limitation of the viewpoint of tracks, carrying capacity of individual vehicles, possibility of stockability etc.
In the second part of the dynamic simulation model it has been created model of handlers´ work on production lines according to input data of handlers´ work which has been gathered from the contarcting authority.
As a relevant simulation period it has been determinated one week.
On the basis of created model there have been created simulation experiments to reduce operational costs o handling and storage – logistic processes which are closely related to the production – and ensure to storage and handlig requirements would be provided in time.
It have been tested 13 variants of simulation experiments focused to eliminate handover places, then 5 variants to eliminate handling technology and a variant to use a new handling vehicle which means removing 4 or 5 old vehicles.
On the basis of Witness outputs it has been proposed an optimization variant which was leading to reduce operational costs.
Results
The basic output from simulation of all proposals was to determinate workload of handling technology.
On the basis of performed changes of removing special combinations of handover places we were able to identificate moves in using of individual vehicles and overall reducing of vehicle using which is caused of reduction of handling.
In case of reduction of number of handling vehicles it is possible to reduce number of workers which brings cost savings 245 000 CZK per month.
In case of investment to a new vehicle and removing (sale) of 4 or 5 old vehicles it is possible a profit up to 250 000 CZK.
At the same time there is a time saving about 15 hours of forklifts work per week.
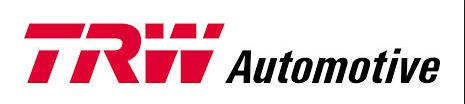
The case study you can download here APPLICATION: Logistic processes optimization BRANCH: Developement, production, and sales of hydraulic brakes SECTOR: Handling BENEFIT: Using the dynamic simulation model in Witness it has been created elimination of some handover places and vehicles number in production with the consequence in decrease of handling and operational costs. Performing these […]