Case study from the automotive industry: A simulation model revealed a big problem
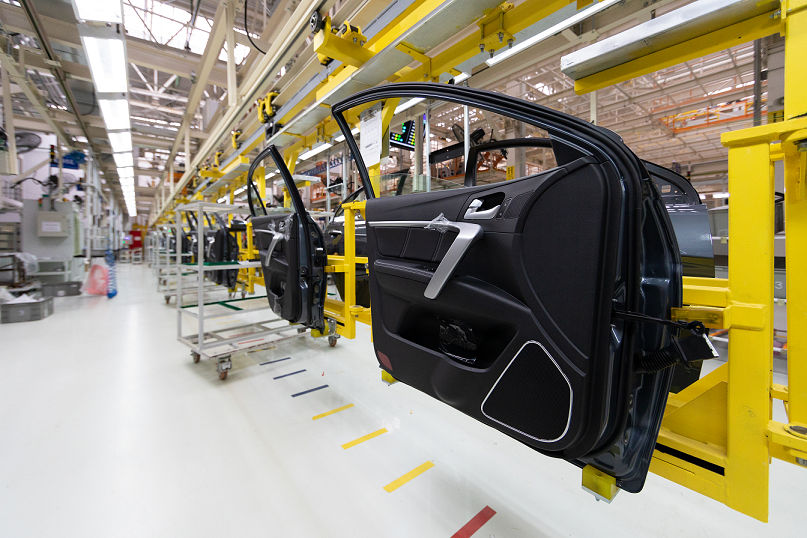
We don’t intend to end 2023 pessimistically; quite the opposite. The project that DYNAMIC FUTURE implemented 8 years ago clearly shows how domestic companies have progressed since then. They think much more ahead. And they verify, for example, the internal logistics of production through simulation. As in the case we describe.
Ensure the flow of the required volume of production
The request, which came from a company producing plastic parts for the Škoda plant in Kvasiny, was clear: We are currently building a new hall with clearly defined dimensions, as well as the layout of the entrance and exit ramps for trucks. And we need to make sure that everything we need can be produced in it. So check the complete logistics of internal processes for us.
“We started from a situation in which it was impossible to change the dimensions of the hall in any way, we could only change the internal arrangement of the production itself, and individual warehouse areas,” describes Jan Šlajer, Company Representative of DYNAMIC FUTURE.
It was about ensuring the flow of the required volume of production within five projects (door panels, plastic bumpers, centre panels, etc.). This was planned for both just-in-time and just-in-sequence, based on customer requirements. For example, it was necessary to determine the warehouses before and after the final assemblies, so that production on the injection moulding machines ran smoothly and in reasonable batches, also taking into account the need for tool changes.
“We Simulated suboptimal production batch sizes, designed warehouse equipment, the locations of specific workplaces, pallet sizes, aisles for handling equipment, and the like. We created seven plant layout variants, and discussed each one with the company’s management,” Jan Šlajer explains.
Estimation versus simulation
The client wasn’t satisfied with the result of the simulation verification of individual variants of the proposals. It turned out that the complex production and demanding logistics based on the needs of the customer for the products was too bulky for the hall being built.
“Thanks to the simulation model, we predicted that the volumes of individual production that the client wanted to realize could not fit into the given space,” states Petr Jalůvka, Company Representative of DYNAMIC FUTURE, adding that the client was firmly convinced of the correctness of his estimates.
The space of the hall didn’t allow for all the necessary processes to be logically arranged, for the manipulations to flow smoothly, and for handling the necessary volumes of production, as well as the requirements for their future growth.
“Our role in such cases is advisory. In short, we state the facts. We prepare a study, and propose a solution. The decision is then in the hands of the competent employees of the companies themselves,” summarizes Petr Jalůvka.
As Jan Šlajer adds, collaborations in which DYNAMIC FUTURE also participates in the selection of the optimal variant of the technical solution, the choice of supplier, and implementation, are no exception.
The company produces, but not in the planned volumes
The previously mentioned customer didn’t consider the dynamic simulation output. And the result? They produce and deliver, but not in such volumes as they had planned. The space for them to grow was also significantly minimized.
“The first major problem was that they asked us late. The second was that they ignored our recommendations. Someone estimated something off the table, calculated the fictitious return on investment in the new hall, and its equipment. During implementation, they discovered that the estimate was not correct, and that they couldn’t count on the original return. But there was no time for changes and modifications,” says Jan Šlajer.
It would have been enough to think through the outputs of the simulation model and propose possible solutions. In this case, for example, renting an external warehouse.
“The company paid the price for an overly ambitious plan and wearing blinders, by blocking future development and, of course, economic
growth,” says Jan Šlajer.
And the conclusion? First the simulations, then the plans
The Company Representatives of DYNAMIC FUTURE agree that since then they have “met” a minimum of like-minded companies. They are mainly approached by customers who plan 2-5 years ahead.
“They want to prepare well for the future, properly plan their next steps, and be clear. Dynamic simulations really help them in this. At the moment, for example, with their help, we’re reviewing projects for Madeta and MP Krásno. Today, no responsible company can get by without a general idea of how much they will have to invest in warehouses and technology,” points out J. Šlajer.
Related articles
Jun 7, 2024
DJI introduces its first delivery drone
DJI introduces its first delivery drone
Jun 7, 2024
5 expert insights into the world of dynamic simulations and logistics
5 expert insights into the world of dynamic simulations and logistics
Apr 2, 2024