How to Handle Material in a Digital Factory: A Move Towards Digital Technology
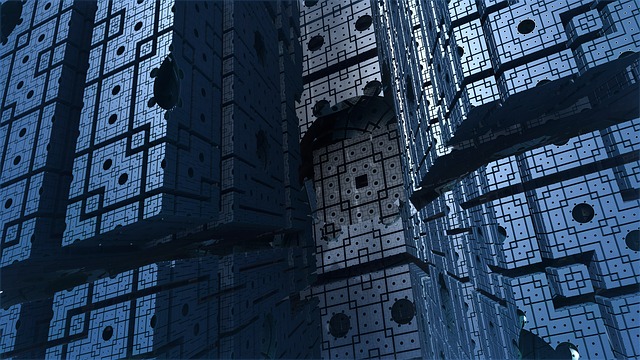
In connection with the ever-increasing use of data analytics in the work process, material handling issues play an important role in the emergence of digital factories.
Just as the demands and expectations of consumers are growing, the material market is growing too. Not long ago, shipments with delivery time of 4 to 6 weeks were part of standard mail transactions. Over time, the Internet appeared on the scene together with a few day delivery. Today, it takes only one day and soon, the ordered goods will be delivered to the current customer’s location within only an hour. Not just their home or office.
It Won’t Work Without a Quality Digital Background
This rapid development requires an adequate infrastructure in order to work. Either huge warehouses or a sufficient number of smaller ones strategically located around where customers are. Or, most likely, a combination of cooperating devices of different range and focus. The flexible and scalable nature of automation tools then enables the support of different types and sizes of warehouses and the overall infrastructure. A key advantage of this solution is the ease of communication between systems and the ability to find the most effective strategies.
Lack of Staff – Room for Technology
Another dominant material handling issue is the critical shortage of staff. This is generally a job that requires a low level of experience, usually removing items from the warehouse for order processing. There are not many people who are interested in working on a night shift or in a freezer and just pushing the boxes with material. Therefore, the trend of robotization is being used today. Robots work with people, making order processing easier and less physically demanding. These robots are very often used in e-commerce. Thus, automation offers one of the ways to face the challenges of finding, training and retaining employees in the enterprise.
Big Data on the Rise
Employee training and retention is a major challenge for the supply and material industries. The growth of automation comes with changes in the demands for this workforce. Employees will need completely different skills, as well as ability to collaborate with the implemented automated systems. The solution for the companies may be to try to work with technical schools to develop educational plan, offer training, practice, workshops, lectures and internships for both students and educators to ensure continuing education for future generations of employees.
Suppliers of the main control systems are mainly integrators who connect large units of individual devices together with software tools for their management. Usually, several companies are involved in large projects and one of them takes over the overall project management. One of the current trends is pairing the product lifecycle management (whatever the nature of the product) with the digital twin of the overall concept and simulating its options and capacity. Digital flows are becoming as important as physical product flows. Finding out about the possibilities of the system in this way is a major strategic point that is moving entire industries forward.
Interest in digitization is currently growing unprecedentedly, and many businesses are seriously thinking about following this “mega-trend” as well. A pretty large number of companies already recognize the advantages associated with the digital twin of their equipment or entire processes. The ability to comprehensively validate the system without having to build it brings significant benefits and savings. Some companies simulate and compare different logistics and supply chain options without having to buy or build anything in advance.
We are witnessing the digitization and analysis of big data pushing the industry towards amazing new horizons.
Related articles
Jun 7, 2024
DJI introduces its first delivery drone
DJI introduces its first delivery drone
Jun 7, 2024
5 expert insights into the world of dynamic simulations and logistics
5 expert insights into the world of dynamic simulations and logistics
Apr 2, 2024