LEGO was among the first, today we have 100+ similar simulations
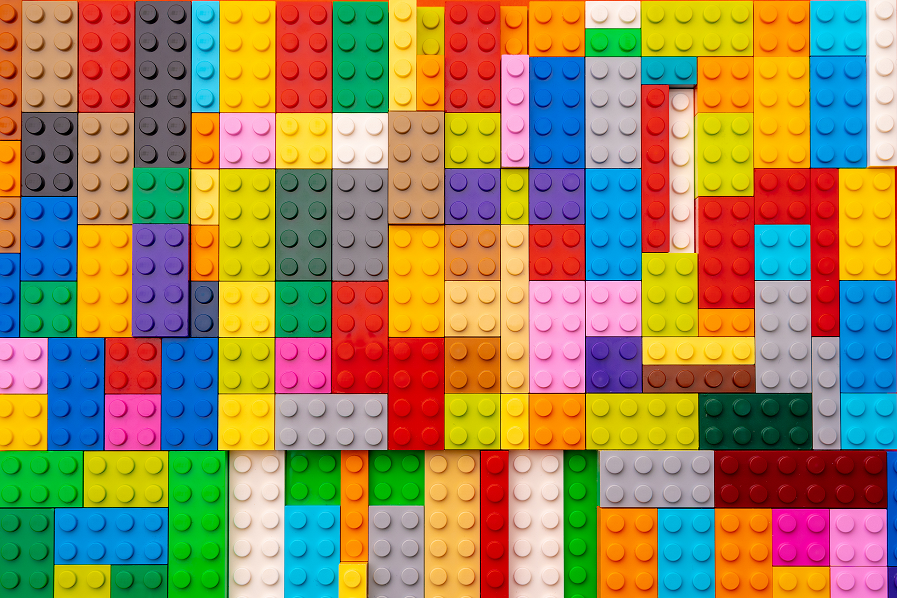
“If the Czech Republic is called the European assembly plant, then I think we are slowly moving towards a European warehouse. Warehouses are growing at a blinding pace, e-shops are trying to ensure the dispatch of goods in the shortest possible time, so they need to deliver them from places as close as possible to the customer,” concludes Jan Šlajer, CEO of DYNAMIC FUTURE.
Verification of storage and handling processes for LEGO
The Prague LEGO warehouse, operated by DHL, ships products worldwide, exactly 22 countries. In 2005, he was one of the first of such size for which DYNAMIC FUTURE was preparing a simulation model. Within the co-operation, it was a solution of the internal arrangement of the building, the size of which was fixed.
“We had to check the warehousing and handling processes, including the design of their optimization in various alternatives. Warehousing processes included shipping, transportation, packaging, assembly, replenishment, transfers, value added activities – co-packs were made – repackaging and inputs. We checked how many workers they needed, verified their productivity and also how many trucks will be needed in the individual parts of the warehousing processes,” describes Jan Šlajer.
In short, the project included a simulation generator for picking and packing, items were divided into several groups, according to turnover, and DYNAMIC FUTURE, based on data obtained from the client, identified a probability distribution, which determined how many items are in the order, and assigned to specific positions.
“We worked with low-lift trucks that managed the picking themselves, packaging and labelling were hand-guided, and electric trucks were used for receiving on the ramps and picking up from the ramps. We also entered time information into the simulation model, for example – how long it takes for employees to check the order, read the packaging instructions, and pack the goods in various ways. We were interested not only in what it was and how long it took, but also in how many times it happened,” says the executive.
Over 30 variants were tested
The resulting layout in the final report shows, among other things, the entire picking and shipping process, which scenarios were simulated, what data was used, and which activities were focused on. “We have identified bottlenecks and capacity problems. We divided the whole model into several parts – the overall warehouse, shipping, picking and packing, supply – i.e. the arrival of goods in the warehouse, with control. And only then did they simulate different variants of possible scenarios. And in the versions of average, minimum, and maximum goods inwards, when we tried to find out what else the warehouse can process,” says Jan Šlajer.
The output of the simulations was the number of required pallet places, racks (including types), picking racks, handling trucks for individual processes, workers, entry and exit ramps, including the assignment of destination countries and items for exit ramps.
A total of 6 scenarios included A-H sub-alternatives, in which the numbers of different trucks and types and uses changed. Then, a change in the picking and packing process was proposed. As part of the assumptions, the simulation also worked with trains that carried pallets, according to the plan. The result was 30 tested variants.
“The whole project took us about 4 months; we did not get any more time from the client. It was a really big and complex space, and today we usually have for similar events about a quarter of a year, and what’s more, we can go into more detail than of course in 2005. In any case, the series of simulations for LEGO was a major project, thanks to which we gained both experience and references. Since then, we have worked for more than a hundred other warehouses,” says Jan Šlajer, CEO of DYNAMIC FUTURE.
Related articles
Jun 7, 2024
DJI introduces its first delivery drone
DJI introduces its first delivery drone
Jun 7, 2024
5 expert insights into the world of dynamic simulations and logistics
5 expert insights into the world of dynamic simulations and logistics
Apr 2, 2024