Pseudo Digital Twin as a Predecessor for Production Capacity Planning
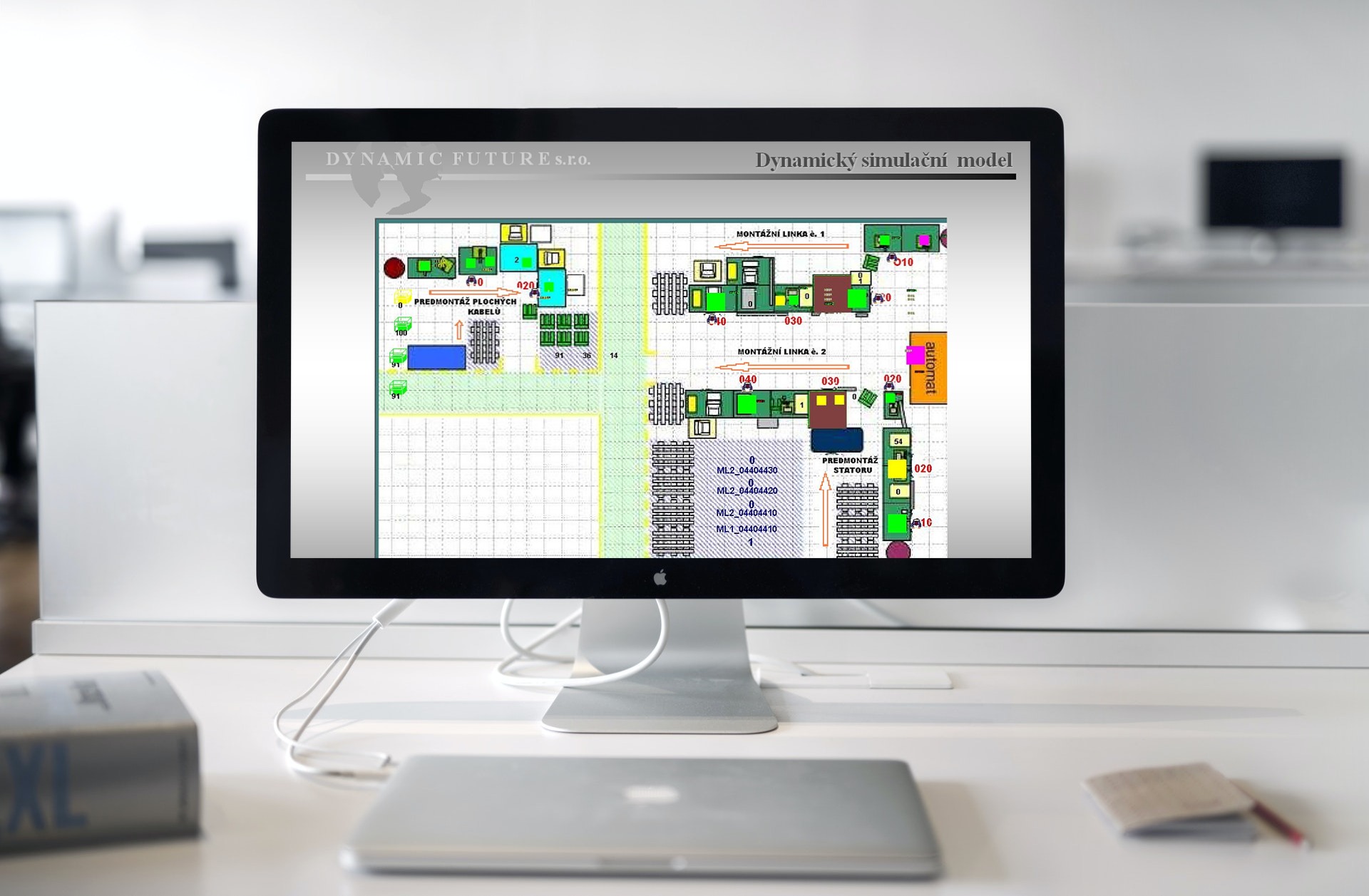
“It was our first use of simulation for operational planning,“ says Jan Slajer about the project that DYNAMIC FUTURE executed for the company KOSTAL CR in 2002. Why do they call it a pseudo digital twin and for how long of a cycle did they prepare the production line’s permeability? This was the first order from the producer of mechatronic components and assemblies for automotive that laid the foundation for our long-term cooperation.
Dynamic simulation models were quite new in our companies. According to J. Slajer, the companies perceived them to be complex like rocket science and only very progressive ones had the courage to use them. KOSTAL CR definitely belonged to those. “It’s important to say that back then, a doctor of philosophy, a person with exceptional outlook and innovative thinking was the executive head. The idea of using our model came from him and proved to be effective,” says J. Slajer.
The project assignment was to create a dynamic simulation model of a B6 flat cable production that is regularly used for steering wheel communication and vehicle control modules. The objective was to increase the permeability of the entire production line, set an optimal status level of semi-finished products in semi-operational warehouses and determine the most suitable number of employees needed to operate the production devices considering the required production ratio of B6 parts. “We analyzed all parts of the production process and identified a bottleneck, in this case, it was a testing room. By adding another testing device, the production went up by 5 %,” explains Petr Jaluvka, the second executive head of DYNAMIC FUTURE.
The way KOSTAL CR cooperated with DYNAMIC FUTURE was exceptional. Every week, the customer sent production requirements to the consulting organization and got its optimal distribution back. “It was a pseudo digital twin, because currently, we create a dynamic simulation model and then hand it over to the client for use. Back then, it was a revolutionary technology, so we performed the simulations for the customer,” says P. Jaluvka while adding that the speed of output delivery was crucial – and DYNAMIC FUTURE had 24 hours for processing and evaluating data.
“We used the WITNESS Optimizer module, where we were setting up the parameters and the module calculated the most suitable solution based on criteria functions. Optimization parameters were: size of the production batch on pre-assembly of flat cables, size of inter-operational supply of flat cables and determination of the operators number. The criteria functions were maximal production in the required structure, maximal workers utilization and the combination of both. Based on these, the most suitable solution was determined,” explains J. Slajer.
From today’s perspective, it’s planning long in advance. For example, food companies plan their production daily, and so are some of the automotive industries.”The ongoing production time is what matters the most. In some cases, just in time is standard, while elsewhere is just in sequence – in this case, the company has four hours to deliver the goods since the order. Cooperation with KOSTAL CR shows where and how quickly the development is moving. The current smart companies work with dynamic simulation models daily and nobody wonders. Twenty years ago, our pseudo digital twin was very progressive and became the beginning of a long-term cooperation,” says J. Slajer.
Related articles
Jun 7, 2024
DJI introduces its first delivery drone
DJI introduces its first delivery drone
Jun 7, 2024
5 expert insights into the world of dynamic simulations and logistics
5 expert insights into the world of dynamic simulations and logistics
Apr 2, 2024