Squeeze the full potential out of your company. A logistics audit will help you
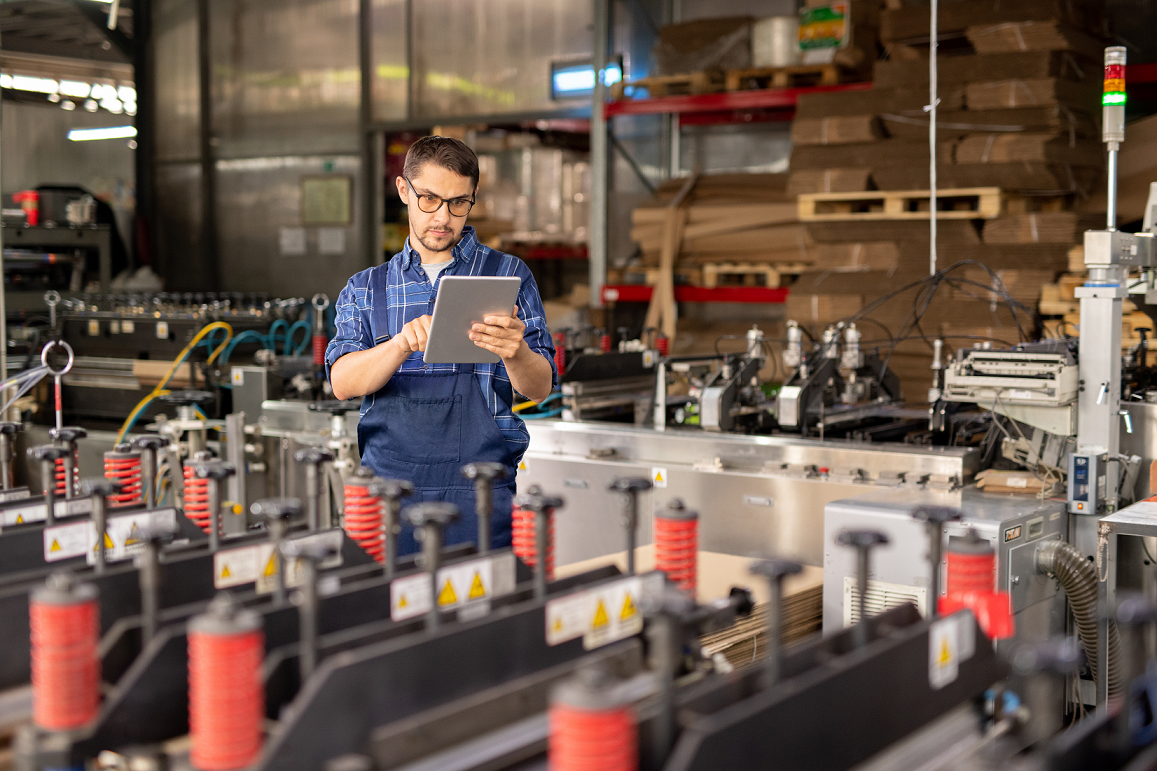
How do you take orders? – Well, electronically. – Specifically? – A business colleague brings them to me once a week, scanned… “Just a few years ago, we had to explain in a complicated way what benefits logistics audit brings to companies. Today, managers are asking about it themselves, and the demand is growing,” states Petr Jalůvka, Managing Director of DYNAMIC FUTURE and Chairman of the Chamber of Logistics Auditors.
If you’re serious, there’s no point in starting with anything else
If DYNAMIC FUTURE usually accepted two to three requests for separate logistics audits per year (not linked to the predictive simulation project), this year their number almost doubled. “The time when the customer preferred to invest in the layout of the new hall and its simulation, rather than focus on optimizing existing strategies, processes, and information support, is apparently slowly disappearing. It’s good, because if I want to change the company, it makes no sense to start with anything else,” says Petr Jalůvka. In his opinion, everyone is aware that it is necessary to maximize the potential that the company has.
Logistics audits usually do not have parameters that can be measured once; changes are clearly demonstrable during a so-called “re-audit”. On the other hand, there are a number of cases where the first audit resulted in a significant streamlining of production or shipping. And companies repeatedly return to some audits even years later, review what has been changed, and move to implement procedures that are not yet effective. By the way, Jan Šlajer, Managing Director of DYNAMIC FUTURE, described in a recent interview how the logistics audit takes place, and what methodology it is based on.
Use what you have, but use it correctly
A frequent impetus for a logistics audit is the preparation for an upgrade or replacement of an information system. It is necessary to examine how the system is used, in terms of functionality.
“We know how the processes should look, and also how they should be supported by the information system. However, it is often the case that the implemented information system does not meet expectations, because the company does not use the functionalities that are integrated in it – they are not implemented, they are implemented poorly, or they are used poorly. Customers are very positive when we tell them: Now it makes no sense for you to buy a new information system just because you can’t use yours,” the Company Representative explains.
When high runners fall to zero
An interesting outcome was the logistics audit that DYNAMIC FUTURE performed for the Kroměříž manufacturer and supplier of fgFORTE batteries. It was a basic analysis of stock movements and sales. Among other things, it pointed to the high runners which, as they say, “dropped to zero” while waiting for the container. Because of this, it always took a few days for sales to return to normal levels.
“It was enough to say as part of the logistics audit that it would be nice to change the purchasing model so that the purchase corresponds with the store. Before I drove home from Kroměříž, the owner called me and wanted me to check a new purchase order. He immediately understood what and how it was necessary to change,” states Petr Jalůvka.
Shipping is also a form of production
And we can also look into history. The former Železárny a drátovny Bohumín (ŽDB), today a part of Třinecké železárny, belongs among those enterprises in which DYNAMIC FUTURE implemented its first projects. Wires for thermal and chemical processing were transported to ŽDB along the tracks, at the end of which were coils with the required physical properties. According to Petr Jalůvka, it was interesting to see how much energy ŽDB invested in receiving input material, and how little added value they gave to the final products.
Specifically, he describes it this way: “At the beginning of the process, we saw optimization and obvious sophistication, including quality control and so on. However, the shipment of final products in old, inadequate facilities was characterized by complicated handling processes. This is how companies with a long history usually work; it is difficult for them to maintain the quality of processes across the entire material flow.”
Of course, logistics providers who consolidate orders and either send them directly to the customer or hand them over to them in their branches show the greatest care for the shipment. Their business depends on it. From the experience of DYNAMIC FUTURE, it follows that in a classic Czech company doing business in any industry, the biggest appeal is placed on production.
“Ninety-five percent of energy is directed by companies into production, with the understanding that the shipping will somehow happen. In their view, shipping is not production. The standard output of a logistics audit is the finding that if the goods do not leave the company well-packaged, consolidated, and with the parameters that the customer expects, the need for repeated orders decreases,” P. Jalůvka points out.
In his opinion, it is absolutely necessary to understand that the process really begins with the acceptance of the order and ends with the acceptance of the product by the customer. A Logistics audit finds weaknesses in the entire chain that companies either don’t admit or don’t even know about.
Related articles
Jun 7, 2024
DJI introduces its first delivery drone
DJI introduces its first delivery drone
Jun 7, 2024
5 expert insights into the world of dynamic simulations and logistics
5 expert insights into the world of dynamic simulations and logistics
Apr 2, 2024