To Find Out Where the Company’s Golden Egg Is
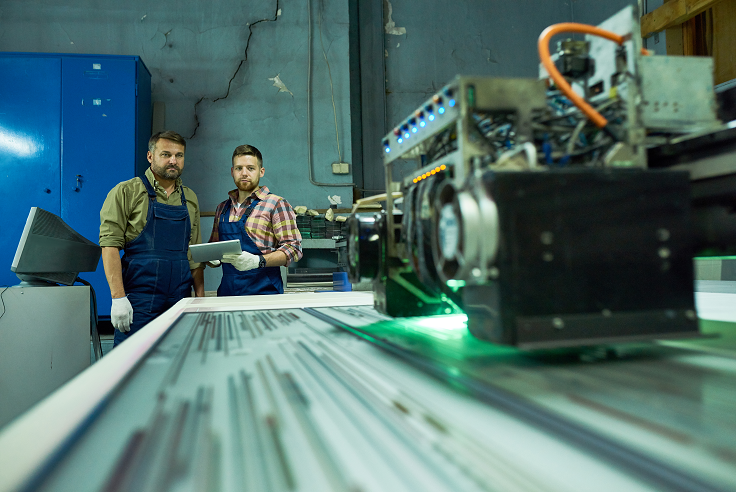
Where is the field of dynamic simulation heading, according to Petr Jalůvka? Why did he change his opinion on augmented reality? And what is easier – to prepare a simulation model or get to know the client’s business perfectly? The executive head of DYNAMIC FUTURE provides a peek into the world of a consulting company that offers a tool for dynamic simulation in production, logistics and organization management.
Online direction
I think that the field of dynamic simulation is moving towards the online environment. Simulations were more about projecting once. The client wanted to change something and needed to decide whether the change would be beneficial. We built a simulation model, simulated scenarios and the client executed the optimal ones in the following years. Today, we project a whole range of digital twins for planning support.
The client wants to know what will happen in the production in the next five days, for example. They go through the processes with a digital twin, tune the needed parameters and can proceed to planning. The next day, they can do the same and therefore work in some kind of routine.
These days, a lot of digital twins are implemented right in the machinery. For example, within a CNC lathe, the simulation of work runs in milliseconds. It seems that the development progresses towards digital twins being used as much as possible.
How far are simulations of entire factories?
To be honest, we haven’t been able to find a partner that would cooperate with us in it. To simulate an entire factory before it is built is not a cheap task to execute. On the other hand, it’s very farsighted. Especially in a time when the prices of building material have gone up so much.
All the needed technologies are at hand. At DYNAMIC FUTURE, we are ready, when it comes to the hardware that these things could be operating on. I believe that within the next two years, we will get a partner and will be able to execute this kind of virtual reality together. And that might not be a production facility. Our philosophy is to start cooperating with universities because of their potential. We just need to get into this area a bit more.
Experts know that many “virtual reality” factories that can be seen on social media are presented with more or less fake videos. 3D modeling can be seen there, as well as some kind of device sequence, but it’s not technically a digital twin. In this model, you won’t start a standard production plan that would be based on the parameters of products, devices, operation, manipulation, buffers… Of course, it seems great, visualization is important, but it’s not the virtual reality that I imagine.
Virtual reality’s added value
Personally, I didn’t see any added value of virtual reality for a long time. It’s nice: I put on glasses, gloves and walk through the factory. However, recently, when me and Jan Slajer invested in the mentioned hardware and started cooperating with our British partner, I started seeing it.
When it comes to big investments, it’s meaningful for the investor to be able to “step into the future”. They can go to the virtual environment, take a look around and reveal whether all the things are the way they imagine. The worst that could happen when building new factories is investing in something that is only on paper. Furthermore, on one paper, there is an object, on the other one, a technology. Every paper is done by another person, the next person takes care of human resources, for example.
Virtual reality provides the possibility to immerse in the operation, take a look at it from the inside and say: alright, that’s just how I imagined it. Or the opposite. You are able to easily reveal classic collision matters – like a forklift being unable to pass through the gate. These are key details. Then, it’s impossible that when the final inspection of the object is carried out, workers come and demolish what interferes or wall up what is missing. This kind of virtual reality utilization makes a lot of sense.
The principles are still the same
The question of whether it’s easier to build a simulation model or understand the business of the client, is of no use. There’s only a handful of principles that this world operates on. Professor Gros always used to say: There’s only one logistics. I’m adding: not only.
When you do the first ten projects, you find out that there are analogies in them. Even though one time, we go to see how rails in ironworks are made and some other time, how marshmallows in a chocolate factory are made, we see the same thing. There are different ingredients, different size of the facility, but absolutely the same technology and production principles. During iron production, various alloying elements are worked with and technological conditions are clearly defined that the workers have to comply with. In the food industry, you work with allergens, as well as their order in production, with colors that can go after one another in order to minimize the need for rebuilding of machines and devices.
We always try to understand the specifics that the business is based on, rather than the business itself. Because no two identical companies in the world are doing it the same. And the key is to understand the deflection. There is a limited range of principles, they can be learned with practice – and the greatest art is to reveal the golden egg of the company.
Related articles
Jun 7, 2024
DJI introduces its first delivery drone
DJI introduces its first delivery drone
Jun 7, 2024
5 expert insights into the world of dynamic simulations and logistics
5 expert insights into the world of dynamic simulations and logistics
Apr 2, 2024