Virtual Tires Are Cost-Saving and Environmentally-Friendly
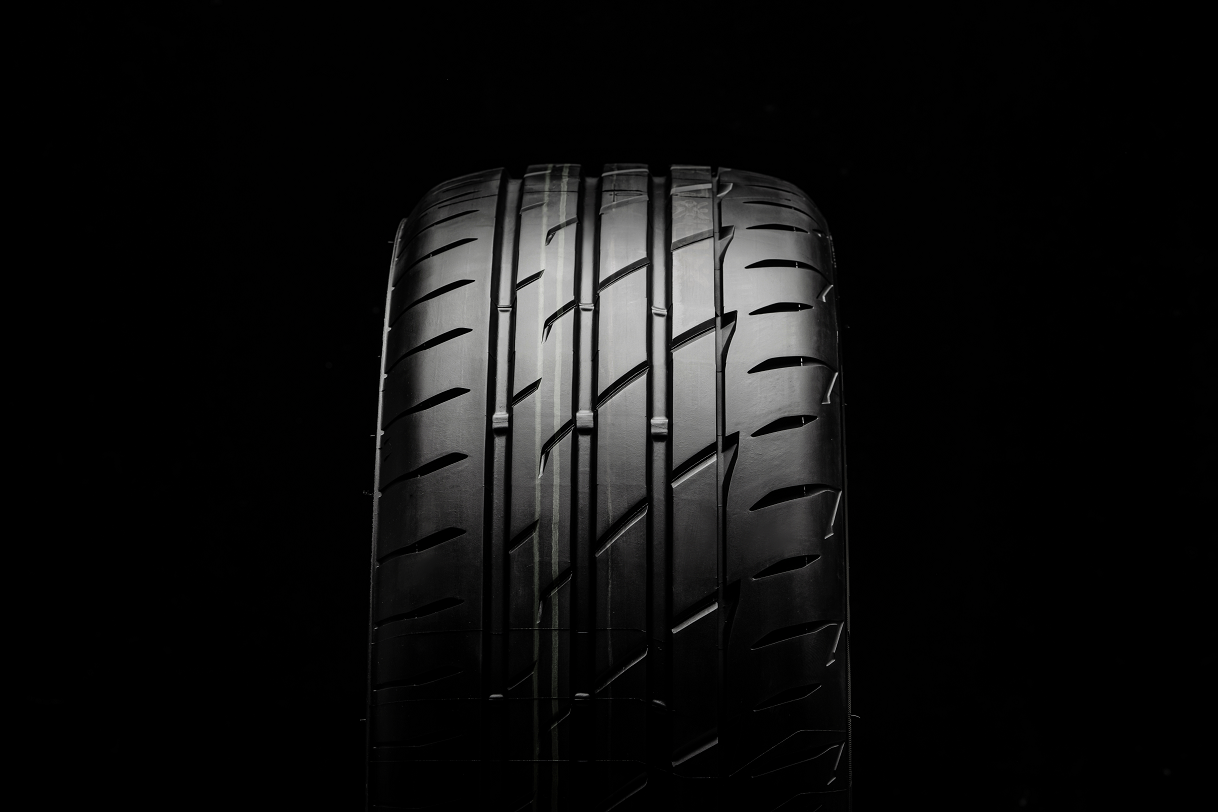
The Japanese rubber gigant perceives virtual tire modeling to be a revolution. Bridgestone considers using this technology a beginning. The company works on more solutions that AI and predictive skills of Advanced Analytics are parts of. The goal is to get and process information about using tires and continually increase their performance.
“Our patented technology of virtual tire development enables us to design a digital tire, test it virtually and tune before producing prototypes and switching to physical testing,” states Bridgestone while emphasizing that this way, the producer gets a lot of benefits. Effectivity and sustainability are considered to be the most important ones. Shortening the time needed to develop is not negligible either, as well as increase in accuracy, as well as flexibility and CO2 emissions reduction.
In every project, Virtual Tire Development saves 200 real tires that don’t have to be produced at all. Thanks to that, Bridgestone saves about 60 % of resources and emissions.
“Our final output is naturally a product for the real world. Therefore, final control with physical tires will always be relevant, but thanks to Virtual Tire Development, physical testing during the development process might be used later on. Traditionally, prototypes of produced tires are tested in a process that requires up to 40 000 km testing on the track”, states the website. High flexibility that virtual tire development enables can test many more variants of a specific product. Digital twin can be adjusted in a second, testing on the simulator is then also really fast. That brings benefits to the environment as well as companies. Shortened development and shorter time needed for testing reduce costs and shorten time of product market launch.
As it’s apparent, digital tire models are very accurate and in complete harmony with the physical ones. Bridgestone integrates the digital twin technology in all of the processes, including developing the most recent premium tires, Bridgestone Potenza Sport.
Related articles
Jun 7, 2024
DJI introduces its first delivery drone
DJI introduces its first delivery drone
Jun 7, 2024
5 expert insights into the world of dynamic simulations and logistics
5 expert insights into the world of dynamic simulations and logistics
Apr 2, 2024