What do you need for a logistics audit? Basically, just time and data
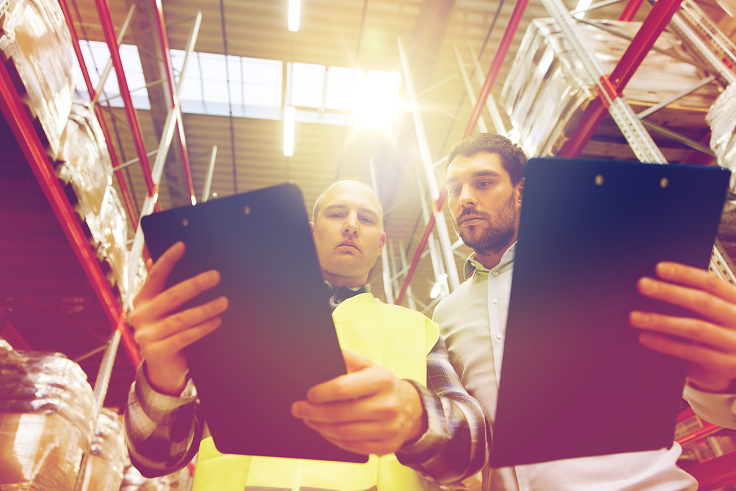
The framework on which the DYNAMIC FUTURE logistics audit specialists build is the same for all companies. If you are facing this process, or are just thinking about it, here are the details of how it works.
The general description of the logistics audit talks about 4 basic steps: setting up a programme with the customer, an interview and measurement in the company, processing the results, and presenting the results with a view to recommending logistical changes. In any case, co-operation between the auditor and the company concerned is essential during the audit.
“In practice, we only need two essential things – time and data,” says Jan Šlajer, DYNAMIC FUTURE Company Representative.
Less than a week, but quite intense
As for the time you will have to spend with the auditors to get enough input information, expect 2 x 2 days. As an example, let’s take a logistics audit in a manufacturing company. Who does the auditor need to interview, and just what does it involve?
- The Sales Office, or place of receipt of orders. The auditor is interested in who and how orders are received, and in what format they are forwarded, for example to purchase orders.
- A Purchasing Manager who describes how his system works.
- The planners explain how they get information, and what software they use. The auditor can thereby assess the continuity of software support, integration, etc.
- Employees in production state how, for example, the plan is transferred from the planner to the Production Manager, from him to the foreman, and on to a specific worker on the shop floor.
- Shift leaders will pass on information about how they order material, and how the material gets to them from the warehouse.
- Logisticians or storekeepers will describe the connection of material receipt, storage, material identification, methods and places of storage, system used for storage, and methods of obtaining information about stored material (according to FIFA or FEFA).
- Expeditors will present the processes of communication with sales, work with order dispatch, cumulation of transport orders, communication with carriers, and method of loading products.
“Of course, it is possible to carry out a logistics audit of only a selected process. Or alternatively the audit of several branches of one company. In principle, it is very similar. All companies have an information system, purchase, sales, storage system, logistics, and the like. And we need to ask about all that,” Petr Jalůvka explains.
Data in standard forms, but from a year ago
The Company Representatives of DYNAMIC FUTURE state that they need to obtain data from the last year from the company for the analysis for the logistics audit. Most often in .xls, .csv, .txt or similar formats. Of course, it always depends on the scope and size of the data, in some cases it is necessary to load them into databases.
“It may happen that it is necessary to supplement the data. I remember the case of a company that neglected to tell us that part of one of its processes is reclassification, where one product becomes another. As part of the analysis, it turned out that for some products the stock levels increased, while for others they decreased. Through an additional inquiry, we discovered that we needed to supplement the missing data,” Jan Šlajer explains.
The magic of a logistics audit
According to Jan Šlajer, this procedure can be applied in all companies. Of course, with modifications reflecting the specific conditions and requirements of specific companies. The most important thing is to capture the uniqueness of a particular business.
“Every company has its own specifics. And this is true even in cases where we compare, for example, companies in the dairy industry producing de facto similar products in a similar way. But it is important to get through the standardization of processes to what makes each one special. That’s the magic of a logistics audit,” Petr Jalůvka states.
Related articles
Jun 7, 2024
DJI introduces its first delivery drone
DJI introduces its first delivery drone
Jun 7, 2024
5 expert insights into the world of dynamic simulations and logistics
5 expert insights into the world of dynamic simulations and logistics
Apr 2, 2024