WMS: Why have it, how to choose it and what not to forget
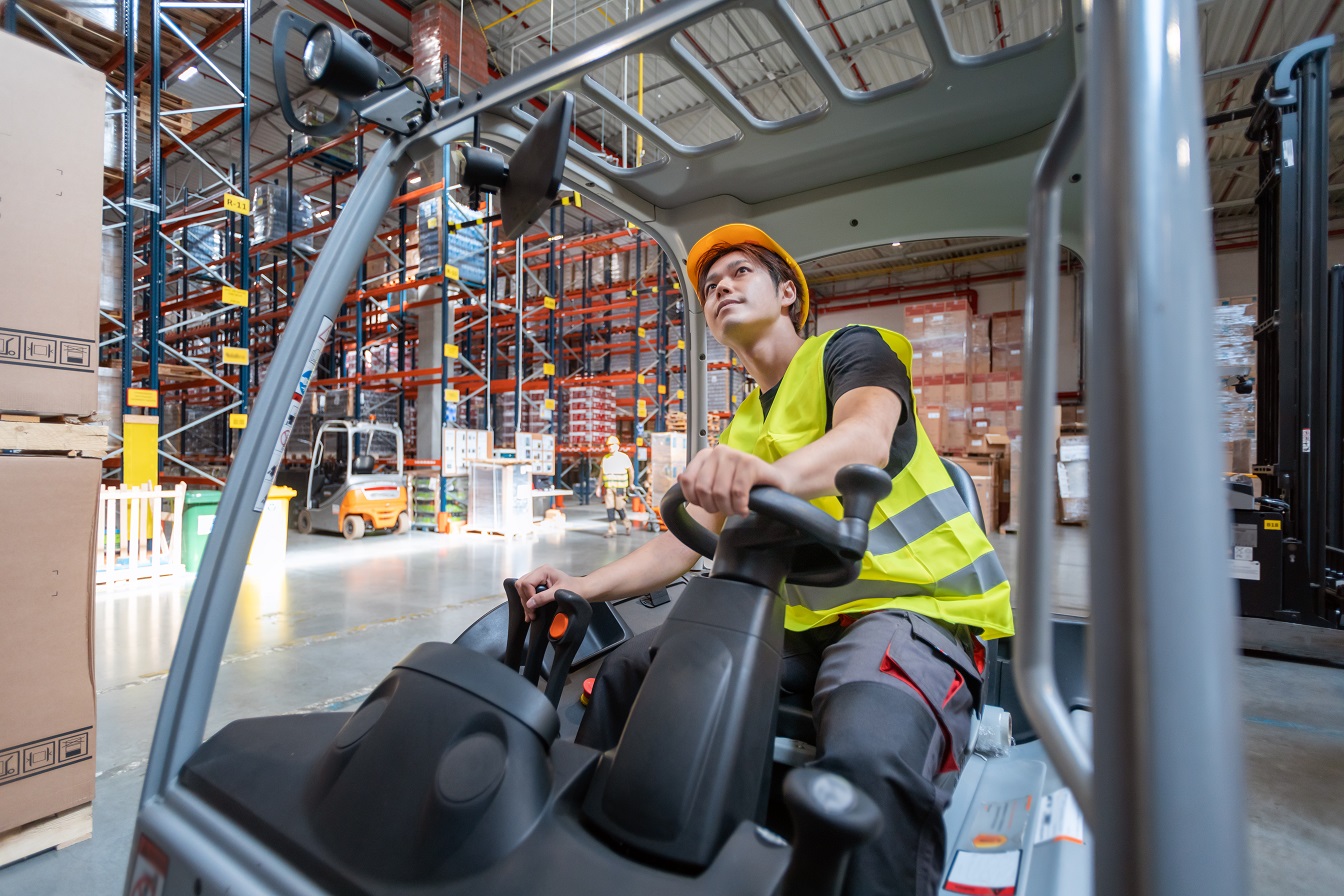
“The Warehouse Management System will not improve processes for companies,” says Jan Šlajer, Company Representative of DYNAMIC FUTURE, at the very beginning of the interview. The practice of his team nevertheless shows that many companies still consider WMS as the “saviour” of unhappy warehouse operations and processes. What is essential when choosing a WMS, when is it worth investing in it, and how can you implement it?
For starters, how do WMS and ERP systems relate to each other?
Jan Šlajer: WMS is a managed warehouse system, and you can purchase it in several variants. There are WMS that are part of the ERP system, and then, of course, external WMS, created outside of the ERP to ensure warehouse efficiency. Whether you go for one or the other option, it’s very important to tell yourself what you expect from WMS, and what it should bring you. Accordingly, either programme the WMS functionality into the ERP system in the form of an algorithm, or choose WMS solo.
Petr Jalůvka: I’ll explain a little more. In my opinion, few people really understand what WMS actually is and what it’s for. People often confuse it with stock records. I would say that I could count on the fingers of one hand the customers who really understand WMS and have it implemented. It usually starts with the business introducing barcode readers. And they report: We’ve implemented a WMS. That’s like saying a shopping cart is a car because it has four wheels. Also, WMS is quite often confused with ERP, which does have a warehouse module that allows you to register warehouse locations and articles (perhaps with the reader), but it is still only about registration.
Why should you consider WMS?
Jan Šlajer: It’s simple – its task is to manage storage and removal as efficiently as possible. Every business needs to satisfy the incoming and outgoing requirements to the maximum extent possible. Typically, an e-shop that buys and sells: orders come in and it has to process them as quickly as possible. Without managing what happens in the warehouse, people will go back and forth on it, choosing what they want and don’t want to do. And this way will never be effective.
Petr Jalůvka: When you need to really manage warehouse operations and processes, then WMS looks for the optimal ways to do it.
Jan Šlajer: I would like to emphasize that it is extremely important to tell myself and know what I expect from WMS, and what it should improve for me. When you want to make processes more efficient and go to WMS, you need the system to support their efficiency, not to preserve it.
How can I choose both the system and its supplier?
Jan Šlajer: Let’s face it, WMS is not cheap. Nevertheless, it is often chosen based on the price. And its implementation and tuning is not a matter of weeks, but rather of months, and sometimes even a year. If you want to improve your processes, you need to know how they currently work before you implement them. You need to know not only the target state, but also the starting state. That’s why we always recommend carrying out a study of existing processes, then a vision of where I want to move them and, based on this information, choose a system. You need to have that vision based on data – for example, we want to go from 21 workers in the warehouse to 15, and we need to reduce the error rate by 25 percent, and so on. You can’t implement a WMS just because you want to have a managed warehouse, but you don’t really know what needs to be improved.
Petr Jalůvka: And something else. Before you start implementing a specific system, go and see a company that already has it. You’ll get much more information and a much better idea than from a sales person’s presentation.
Try to describe an example where the implementation od WMS was successful, and made the warehouse significantly more efficient.
Jan Šlajer: Hortim opened a completely new warehouse in Slovakia, and Anasoft supplied them with WMS. heir system is built on a digital twin, so they manage that physical flow through it. We at DYNAMIC FUTURE processed a study with process designs for Hortim, and Anasoft set up the WMS based on this. We examined, for example, reducing the number of pickers from 19 to 14, with gradual changes and adjustments in order to achieve the desired parameters. We found that there were delays in the picking zone because it was not replenished properly. So the system had to be refined in such a way that the waiting times disappeared. We also dealt with storage in a refrigerated warehouse, unloading on full pallets, two picking zones for picking cardboard and goods by the kilo. It was a very nice collaboration, with a great result.
Does DYNAMIC FUTURE regularly participate in such projects?
Petr Jalůvka: At Hortim, we set up the processes and designed the entire solution. The WMS was then set up and implemented according to their requirements. We routinely audit and set up processes. As consultants, we also help with the definition of WMS requirements.
Jan Šlajer: The same work also awaits us for other customers. We set up the processes of how the WMS should work, then create the requirements or specifications that the system should meet. Basically, we are able to help companies both with the selection of WMS itself, and with implementation, and we can manage it for them.
Related articles
Jun 7, 2024
DJI introduces its first delivery drone
DJI introduces its first delivery drone
Jun 7, 2024
5 expert insights into the world of dynamic simulations and logistics
5 expert insights into the world of dynamic simulations and logistics
Apr 2, 2024