Jeden z prvních projektů DYNAMIC FUTURE aneb Simulace před 20 lety a dnes
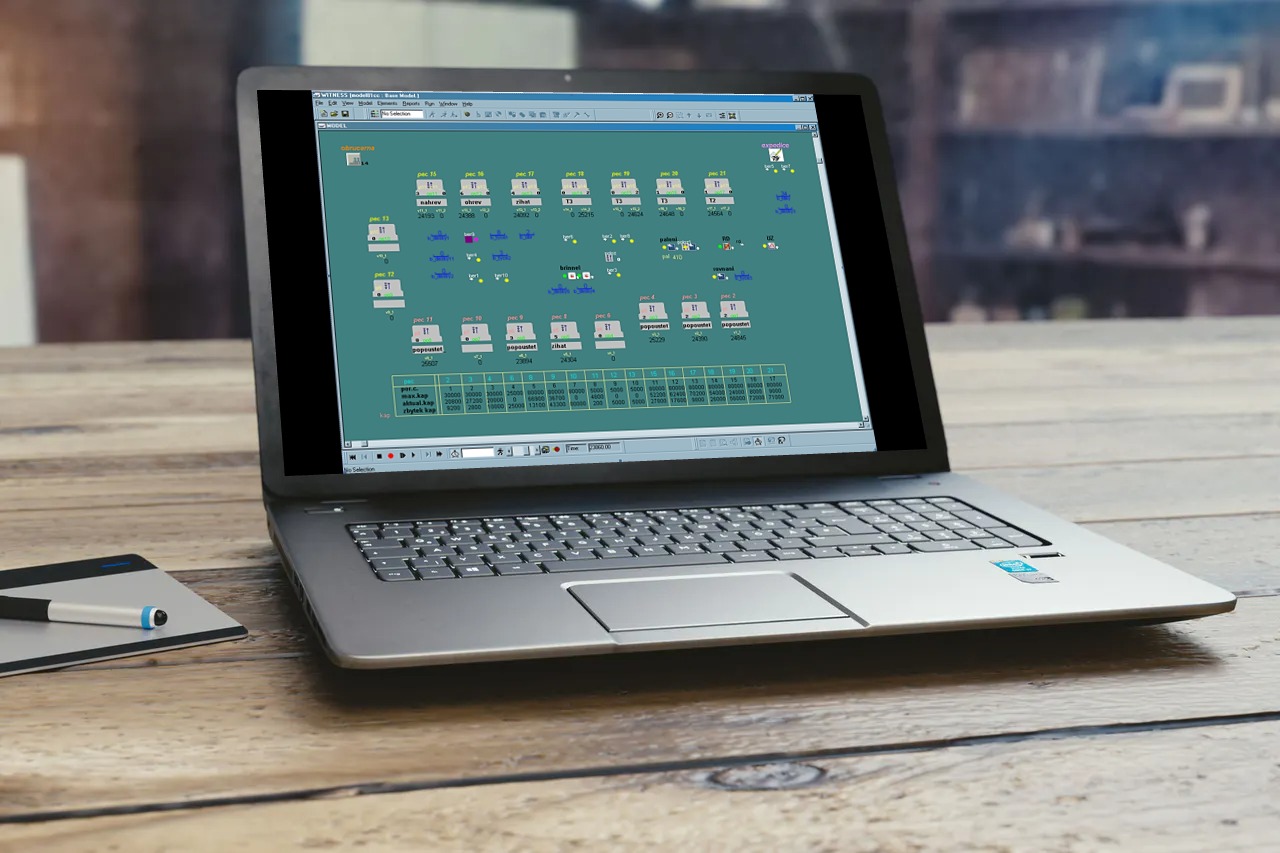
„Tehdy nás oslovovali jen velcí vizionáři,“ říká o době před dvaceti lety, kdy DYNAMIC FUTURE na trhu začínala, Petr Jalůvka, jeden z jednatelů. Stojí zato podívat se zpátky a srovnat, jak digitální dvojčata vypadala tenkrát a jak vypadají dnes. Tady je krátké připomenutí projektu Kovárna Kunčice.
Kovárna se složitou technologií
Zadání stanovilo jako cíl zvýšení propustnosti a plánování kusové výroby jednoho z úseků provozu kovárna, a to s pomocí vytvoření simulačního modelu sestaveného v prostředí Witness. Zákazník potřeboval navýšit kapacitu na kovárně, tedy zvýšit její propustnost. Chtěl získat analýzu využití lisu, nalézt úzká místa výroby, minimalizovat prostory k ní potřebné a stanovit propustnost linky s ohledem na výrobkovou skladbu a směnnost. Zároveň také požadoval snížení počtu zaměstnanců, a to o 40 %.
„Bylo potřeba pracovat s poměrně složitou technologií – kovárna měla několik typů pecí. Před každým kováním se musel výkovek nahřát. Jenže při velikosti výkovků se koval jeden produkt i na několikrát, takže se zase vše rychle ochlazovalo. Vykování jednoho kusu byla poměrně dlouhá procedura, z níž nejvíc času zabral právě ohřev pecí,“ říká Jan Šlajer, druhý z jednatelů DYNAMIC FUTURE. Kolega dodává, že díky tomuto zjištění také prověřovali investici do rekonstrukce jedné z pecí: „Na základě výstupů z našeho modelu nakonec kovárna investici zrealizovala.“
Bez digitálních dat
Na úplném začátku stála datová analýza (dnes se provádí logistický audit), která v roce 2000 nebyla úplně snadnou záležitostí. „V případě kovárny jsme neměli k dispozici žádná digitální data, všechno bylo zapsáno v pecních knihách. A ty se musely ručně přepsat do počítače. Atypické také bylo, že kovárna se zaměřovala na zakázkovou výrobu a součástí zadání bylo snížit počet jejích zaměstnanců. S tak razantním požadavkem se v dnešní době už nesetkáváme,“ uvádí Petr Jalůvka.
DYNAMIC FUTURE vytvořila model daného úseku kovárny v programu Witness 2000 tak, že v něm bylo možné sledovat jednotlivé výrobní pece s ostatními úseky a na nich probíhající operace vázané na konkrétní výrobek. Tabelována byla naplněnost jednotlivých pecí, jejich volná kapacita a využití ostatních pracovišť. Soustava proměnných umožnila měnit dobu zpracování výrobků na jednotlivých stanovištích (dobu pobytu v pecích, dobu pálení tvaru apod.) a simulovat tak spojování různých výrobků se stejnou technologií do skupin nebo měnit technologii zpracování (teplotní diagramy atd.).
„Vazba představ a reality byla tehdy velmi nepřímá. Když chlapi vykázali, že udělali tolik a tolik tun, nikdo o tom nepochyboval. Když jsme přišli s digitálním modelem a analyzovali tvrdá data, získal management firmy úplně nový pohled. Pokud někdo ve fabrice tvrdil, že jednou mu výrobek zabere nějaký čas a jindy desetkrát delší, ptali jsme se proč. Hledali jsme manipulace navíc, uměli je ohodnotit a velice rychle zařadit mezi sledované prvky systému. Pomohli jsme tím rozkrýt provozní slepotu, která v každé firmě historicky vzniká,“ popisuje P. Jalůvka.
Optimalizace plánu výroby přinesla výsledky
Model digitálního dvojčete v tomto konkrétním případě poukázal na faktory ovlivňující výrobu. Patřil k nim mimo jiné velmi rozmanitý sortiment výrobků od několika dodavatelů, různá technologická zpracování různých produktů, možnost výskytu skrytých poruch a tedy nutnost opakovat některé operace, nízká informovanost o přicházejících výrobcích komplikující plánování, výskyt vad a čekání na přejímače a výsledky zkoušek. To všechno snižovalo propustnost výroby. „Prvním výstupem bylo doporučení kroků ke zvýšení zmíněné propustnosti, druhým pak průběžná práce na optimalizaci výroby. Zákazník nám posílal požadavky, my jsme je projeli modelem ve Witness a poslali mu optimální plán výroby. Jak ji má složit, aby měl celou kovárnu co nejlépe vytíženou a dosáhl propustnosti, jakou potřebuje, a splnil zákazníkům požadavky, které očekávají,“ popisuje J. Šlajer.
Výsledky? Mimo jiné snížení doby, kterou tráví výrobky v lisovacích pecích o 3 % za 2 měsíce, tedy o 859 hodin; zkrácení doby výroby vrtulové hřídele v průměru o 54 %, zvýšení počtu expedovaných výrobků o 9,5 %, růst využití lisu o 7,2 %.
Model byl navázán na excelovský soubor (nebo podobné vstupní soubory) se strukturou vytvořenou odborníky v DYNAMIC FUTURE. Pro zákazníka šlo o uživatelsky nekomfortní prostředí, proto si nechával analýzy zpracovávat externě u DYNAMIC FUTURE.
Digitální dvojčata jako aplikace
„Současná digitální dvojčata mají trochu jinou rovinu,“ říká P. Jalůvka s tím, že pro zmapování výkonu se dnes používají MES systémy a podobně: „Moderní procesy jsou obklíčené řadou čidel, zisk dat je tedy nesrovnatelně snazší. Druhou změnou je způsob, jakým může zákazník se simulačním modelem pracovat – vytváříme pro něj standardizovaný model Manager, v jehož rámci si dohodneme, jak do něj bude klient dodávat vstupní data, jak budou vypadat… A v podstatě mu dodáme aplikaci, ve které si simulační model ovládá sám. Stačí, když má koupenou licenci Witness Viewer.“
Zákazník tak dostává do ruky nástroj, díky němuž si může jakoukoli změnu, která se v procesech jeho firmy děje nebo může dít, prosimulovat a prověřit sám. Bez toho, aby se musel obracet na DYNAMIC FUTURE a stálo ho to další finance.
Výsledek je ovšem stejný tehdy jako dnes: zefektivnění procesů, snížení prostojů a zmetkovitosti, zvýšení propustnosti výroby, optimalizace nákladů.
Související články
Čvc 11, 2024
Aplikace pro WMS? Vysoká efektivita, rychlé aktualizace, maximální variabilnost
Aplikace pro WMS? Vysoká efektivita, rychlé aktualizace, maximální variabilnost
Čvn 7, 2024
Setkání uživatelů nástroje PREWIT
Setkání uživatelů nástroje PREWIT
Čvn 7, 2024